Key Points/Overview
Phosgene is an important chemical intermediate used in the process to manufacture a variety of industrial and consumer products. Phosgene is produced by reacting carbon monoxide with chlorine in the presence of a catalyst.
Phosgene is nonflammable and by itself does not present the dangers of explosion or fire that can occur with other materials. Because phosgene liquefies at 47°F, it can be easily cooled and condensed into a liquid for improved handling.
In finished end products evolving from chemical processes where phosgene was a reactant, analysis indicates there is no residual or un-reacted phosgene present to consumers in the end product.
Uses & Benefits
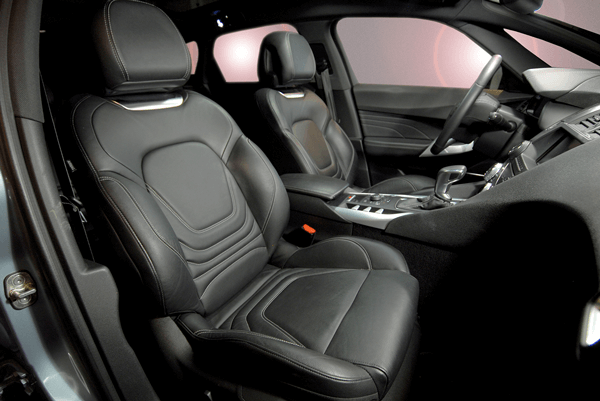
Industrial Applications
Phosgene is important in manufacturing coatings, adhesives, sealants, and elastomers used on floors and automotive interiors. It is also used to make polycarbonate plastics and specialty chemical intermediates.
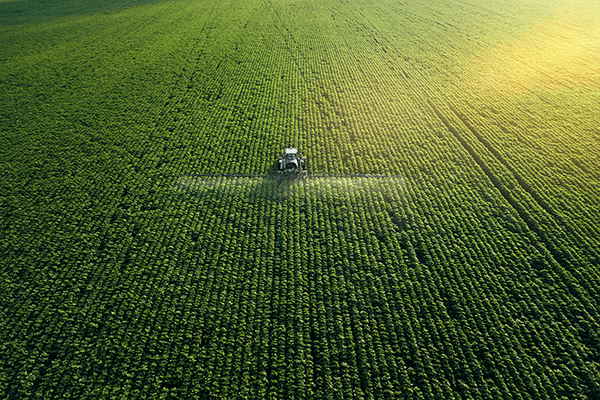
Agricultural Applications
Phosgene is used as a component in fertilizer to enhance crop yields and quality. Phosgene is also used in the synthesis of some herbicides and pesticides.
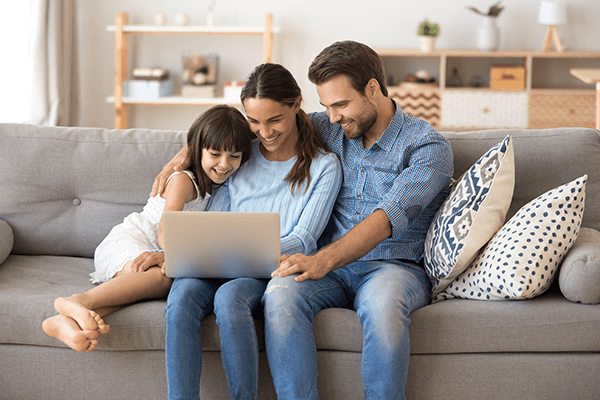
Consumer Products
Phosgene is a building block chemical in the manufacture of diisocyanate chemicals used to make a range of polyurethane products used in everyday life, including flexible foam in upholstered furniture, rigid foam as insulation in walls and roofs, and thermoplastic polyurethane used in medical devices and footwear.
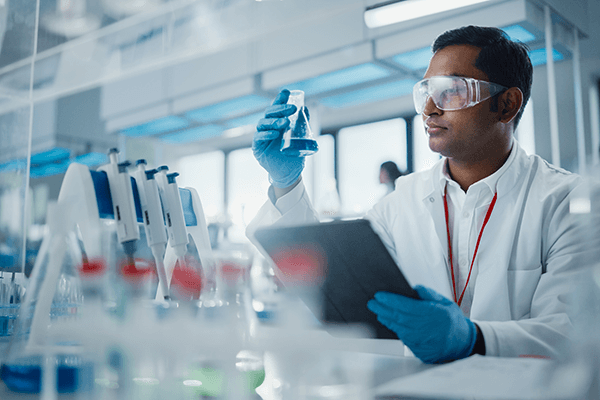
Safety Information
A few federal agencies have provided recommendations for exposure limits for phosgene. According to the Occupational Safety and Health Administration, the recommended exposure limit is 0.1 parts per million (ppm) averaged over an 8-hour work shift.1 The National Institute for Occupational Safety & Health has recommended the airborne exposure limit is 0.1 ppm averaged over a 10-hour work shift and to not exceed 0.2 ppm during any 15-minute work period.2
To protect workers and the community, companies that make and use phosgene take precautions in the form of plant design, operator training, chemical handling training, safety procedures, area and personal monitoring, emergency action plans, and warning systems.3
Facilities that handle phosgene undertake a variety of safety measures to prevent phosgene releases. Manufacturers install items such as seal-less pumps, non-intrusive instrumentation, plant enclosures, remote isolation valves, neutralization scrubbers and curtains, corrosion monitoring systems, and vacuum systems at their facilities, as appropriate, to mitigate risk.
Designated plant personnel are responsible for directing appropriate actions to be taken during phosgene emergencies. Manufacturers have developed emergency plans for use in the event of a process upset or phosgene release. These plans normally include corrective actions and community notification procedures. Plant management and local authorities work together to formulate how the appropriate community notification will be given.
In finished end products evolving from chemical processes where phosgene was a reactant, analysis indicates there is no residual or un-reacted phosgene present to consumers in the end product.
Sources
- https://www.osha.gov/annotated-pels/table-z-1 and https://nj.gov/health/eoh/rtkweb/documents/fs/1510.pdf
- https://www.cdc.gov/niosh/idlh/75445.html and https://nj.gov/health/eoh/rtkweb/documents/fs/1510.pdf
- http://www.epa.gov/emergencies/content/rmp/index.htm
- https://www.atsdr.cdc.gov/toxfaqs/tfacts176.pdf