Key Points/Overview
Methacrylates add rigidity and durability to polymers and plastics found in dental prosthetics, bus stop shelters, road marking paints, and many other applications.
Methacrylates have a low toxicity and consumers are unlikely to come into direct contact with them in their raw form.
In manufacturing settings, people who work with this material may experience irritation, an allergic reaction, or asthma trigger. OSHA has defined a permissible exposure limit for methyl methacrylate in industrial workplace settings.
Uses & Benefits
Methacrylates are used in a range of industries and applications, including:
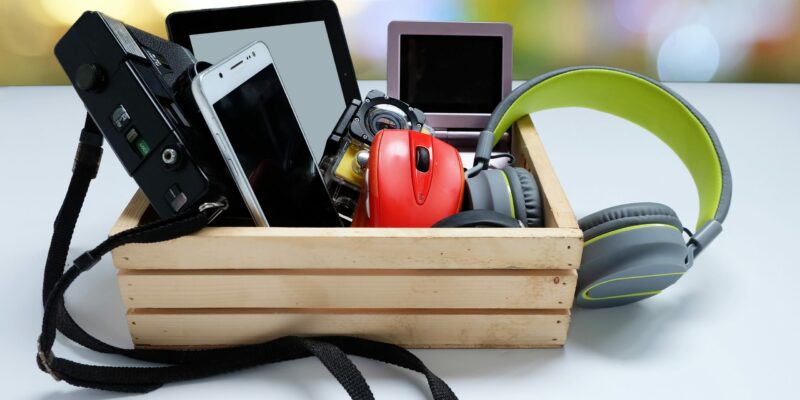
Electronics and Computers
The electronics and computer industries use methacrylate-based polymers to manufacture flat-screen computer monitors and televisions, as well as in DVDs, compact discs and laser discs. Printed circuit board coatings also contain methacrylate polymers, which can provide them with increased resistance to corrosion, prolonging their service life.
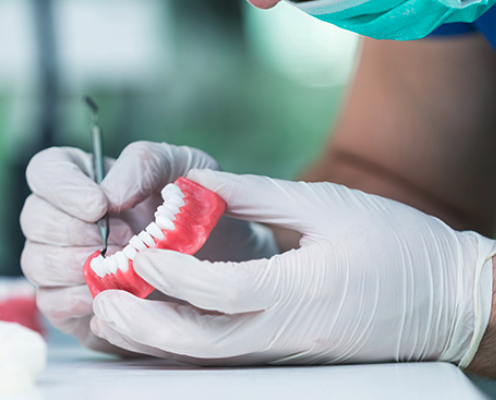
Medical and Dental Applications
Methacrylate-based polymers are used to manufacture a wide range of medical equipment and other medical and dental applications where purity and stability are critical – from intravenous (IV) tubing connectors, medical pump and filter housings and heart valves, to hyperbaric chambers and baby incubators, artificial teeth, dentures, bridges and dental prosthetics. Cements containing methacrylate-based polymers and liquid monomer are used by physicians in hip replacements and by dentists in white dental fillings with liquid monomers polymerized in situ.

Acrylic Cast and Extruded Sheets
Polymethylmethacrylate (PMMA) and PMMA-based sheets help form shatter-resistant, clear and colored sheets for building windows, skylights, bus shelters, bullet proof security barriers, signs and retail displays, among other applications. PMMA also can be used with a mineral filler to make artificial stone for kitchen and bath countertops and sinks.
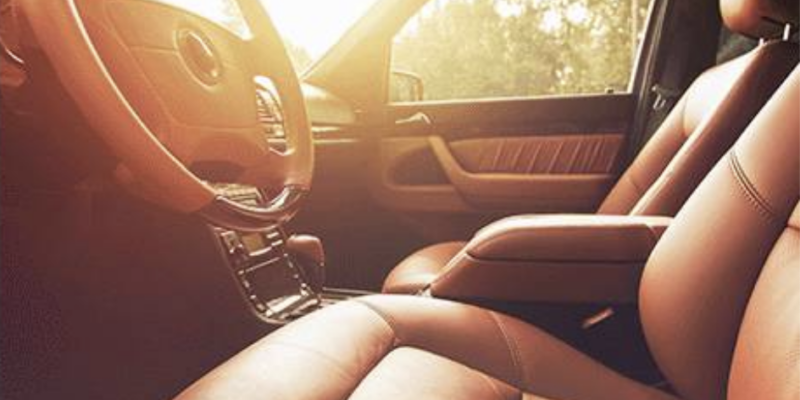
Acrylic Resin
Beads or pellets made from methacrylate-based polymers can be molded into many other end use articles, such as taillights and instrument clusters for cars and trucks, knobs on sink faucets and other home appliances, and light lenses in commercial buildings and airport landing lights.
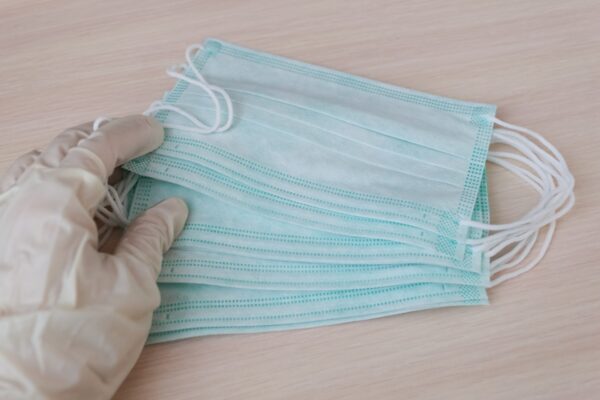
Safety Information
Consumer exposure to methacrylate monomers from finished products made with methacrylate-based polymers is typically very low, and both oral and dermal exposures under normal use are considered to be negligible.
In some products like glues or cements, varnishes or other finishes, consumers may be exposed to liquid monomers until the adhesive or coating cures or dries. For these materials, package labels provide safety information, including instructions to use the product in a well ventilated area and prevent skin contact.
Exposure to methacrylate monomers is most likely to occur through worker inhalation and skin contact during production, transportation or use of these compounds. The U.S. Occupational Safety & Health Administration (OSHA) has defined a Permissible Exposure Limit (PEL) for methyl methacrylate of 100 parts per million (ppm) for an 8-hour time-weighted average, or the average value of an exposure over an 8-hour work shift.